Thermoformed Blister Product Defects
By Hope Chan. Last updated: Sep. 1st, 2022
As one of the top-ranked go-to packaging solutions, custom thermoformed blister products are often seen in our daily lives. But just like any other items, there are defects in blister packs. Then what are they and what do they look like?
Keep reading and you shall find out.
Table of Contents
1. Pulling Line Deformation
Pulling Line Deformation is known as ‘拉线’(La Xian) in Chinese. It causes a slight change in shape or configuration of the blister pack.
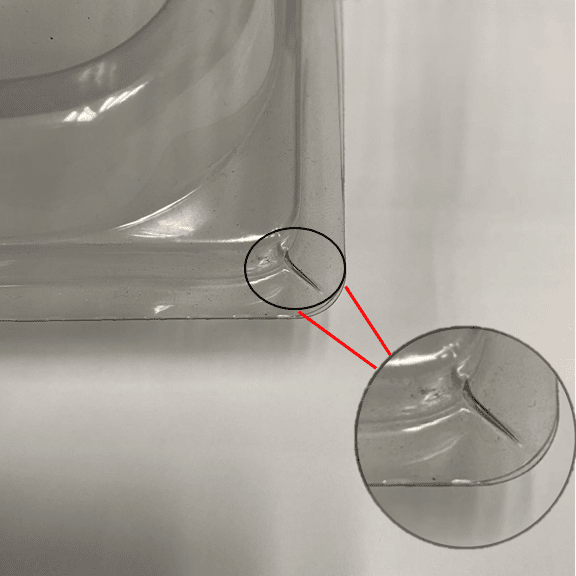
As you can see from the photo, it is an undesired line-shaped protrusion appeared on the surface of the blister pack.
Some might not be bothered by it, but most find it visually unacceptable.
So products with pulling line deformation are often considered flawed and cast aside.
2. Inconsistency in Thickness
Just as the term suggested, blister products with this type of defect are uneven in thickness.
This is caused by inadequate or inconsistent vacuum venting during the thermoforming process, which in the end leads to thickness inconsistency.
Undoubtedly, this is also an unwanted characteristic in blister products.
3. Doformation
This can occur during production and during transportation.
>> Suction Insufficiency
This situation tends to occur when temperature isn’t controlled properly, resulting in part of the blister pack body not being fully sucked (or thermoformed) to its intended place or degree.
In other words, suction insufficiency often causes dimensional inconsistency and forms warped parts, which may not be functional and unable to contain custom-shaped items.
>> Compressional Deformation
During transportation or unloading, there is always a possibility of the cartons being crushed or not strong enough to stand rough handling, thereby causing deformation to the blister packs.
But don’t worry, you can always work something out with your supplier: arrange for a new batch of goods to be shipped to you right away, make up for the damaged ones in the next order, or simply get a compension for the broken ones.
4. Scratches
There are bound to be a few scratch marks on mass production products.
After the thermoformed plastic sheets are die-cut into a smaller form to make them the desired size and shape, these smaller individual blister packs will then be piled up and waited to be stacked in rows. So some of the final products will inevitably have a few scratches.
For buyers that are detail-oriented and won’t settle for less, it’s suggested that you made your needs known so that your manufacturer can take out all of the flawed products before packing.
5. Trapped Dust
During the production process, some fine dust in the air might accidentally drop on the heated plastic sheets, hence resulting in trapped dust defect.
It appears in the form of tiny air bubbles and most will find it acceptable. But if the bubble is too big to be ignored, then the blister pack should be considered defective and removed.
6. Lack of Clarity
Sometimes during the thermoforming process, when temperature isn’t controlled properly, along with inconsistent or inadequate venting, the surface of the blister packs will appeal to be foggy, unclear and even a bit white-ish.
So products with features like lack of clarity are considered flawed and will definitely be removed from the batch.
7. Jagged Edges
This can happen when the die-cut knife tools are blunt, resulting in rough and jagged edges.
As you can see from the 2 photos shown below, some suppliers don’t really deliver good quality products. By GoalPackaging standards, blister packaging products are defective if they have rough or rugged edges. We always make sure our products get clean edges. No jagged edges, sharp corners, or pointy bumps.
There you have it. The total 7 common defects you can find in blister products.